Courant 2025, l’usine automobile Stellantis de Sochaux inaugurera l’ouverture du premier atelier de peinture neutre en carbone dans le monde.
Ce n’est pas anodin que cela se passe à Sochaux où, il y a plus de 100 ans, naissait le premier atelier de carrosserie de la marque déjà capable de sortir 100 véhicules par jour ! L’histoire de ce site ne fera qu’évoluer avec le temps, les progrès technologiques, et dans une gabegie d’énergie plus ou moins maîtrisée. Or, depuis des années, les constructeurs automobiles comme Stellantis ont bien pris conscience qu’il fallait réduire les consommations d’énergie, à la fois pour la planète, et sans aucun doute pour mieux maîtriser les coûts et donc la marge finale. Qu’importe les raisons car, si pour satisfaire les actionnaires, il faut dans le même temps réduire les émissions de gaz à effet de serre, c’est toujours ça de gagné !
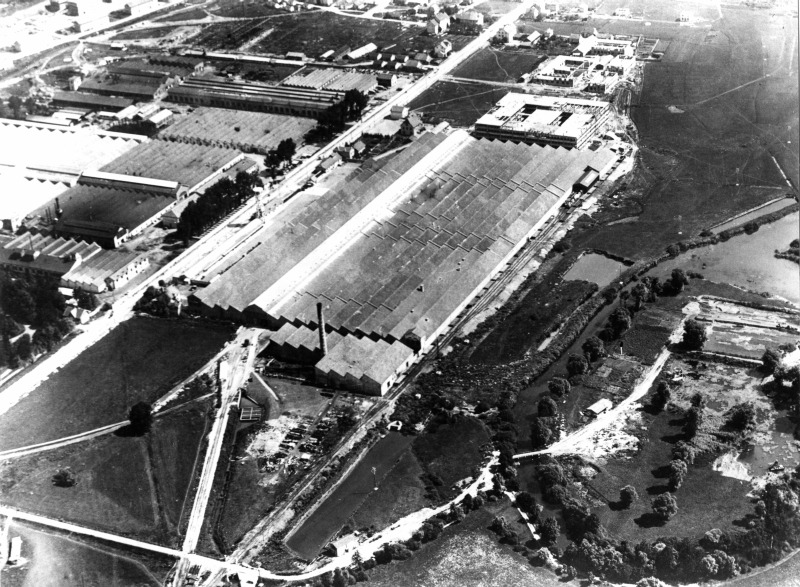

Les premiers visés sont les ateliers de peinture car ils génèrent pratiquement 65 % des émissions totales de CO2 d’une usine automobile et sont, par ailleurs, de grands consommateurs d’énergie et d’eau. Alors, lorsque Stellantis annonce son ambition de devenir “carbon net zero” d’ici 2038, cela passe obligatoirement par ce chemin. “Grâce à une transformation ambitieuse, les ateliers de peinture de Stellantis ont déjà réduit leur consommation d’énergie de 27 % par rapport à 2021. Ils visent une réduction de 50 % d’ici à la fin de 2025 pour atteindre une moyenne de 321 kWh/véhicule”, indique le service communication de l’entreprise.
Pour parvenir à cet objectif ambitieux, les équipes peinture du groupe ont identifié trois domaines clés de transformation pour des actions immédiates et à moyen terme.
Le premier consiste à diminuer le nombre d’opérations de cuisson pendant le processus de peinture avec la technique dite 4-Wet qui permet d’appliquer 4 revêtements avec seulement 2 fours de durcissement, contrairement au processus actuel 2-Wet qui nécessite de sécher chaque revêtement avec 4 fours à gaz qui consomment de l’énergie. Déjà, de nombreux ateliers du groupe utilisent cette technique 4-Wet comme en Pologne avec une consommation réduite à seulement 245 kWh/véhicule. 14 autres ateliers dont 9 en Europe, 3 en Amérique du Nord et 2 en Amérique du Sud seront à même d’utiliser cette technique d’ici à fin 2024.
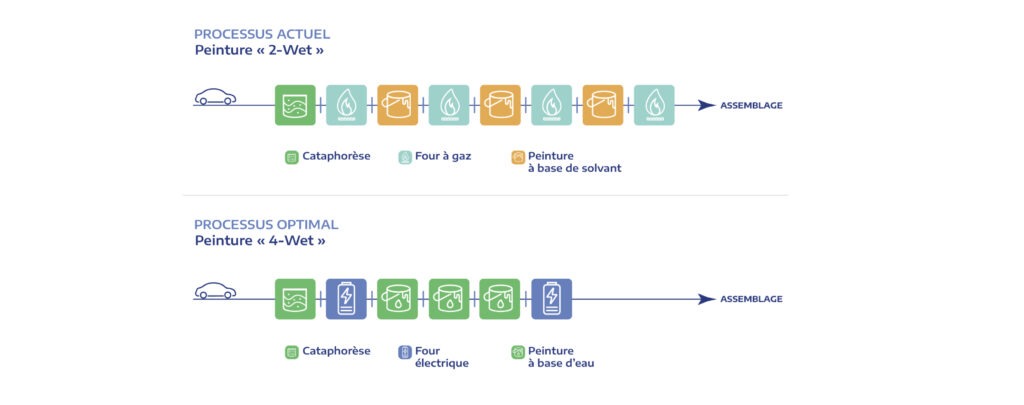
Le deuxième axe porte sur l’électrification des ateliers de peinture comme autre facteur de réduction des émissions de CO2. Traditionnellement, les fours sont alimentés au gaz naturel. Les nouveaux ateliers sont construits avec des fours électriques. En parallèle, les fours existants passent d’une alimentation au gaz naturel à l’électricité verte ou renouvelable. “L’impact du passage du gaz naturel à l’électricité pour les fours de cuisson est encore plus significatif lorsque de l’électricité verte (photovoltaïque, éolienne, géothermique et biomasse) est achetée ou autoproduite sur les toits de nos usines”, souligne la communication de Stellantis qui rajoute : “Notre programme prévoit de synchroniser le plan de transformation de l’électrification de chaque usine avec le plan d’autonomie énergétique de l’entreprise afin de couvrir 75 % des ateliers de peinture”.
Le troisième axe porte sur l’utilisation de nouveaux matériaux que les équipes peinture de Stellantis ont développé avec une nouvelle génération de peintures et d’e-coats* à basse température de cuisson, offrant ainsi à plusieurs usines de nouvelles possibilités de réduire leurs émissions de CO2. La première utilisation a été faite en France où elle a permis de réaliser d’importantes économies d’énergie et de réduire les coûts.
Et la communication de Stellantis de conclure par ces mots : “Ces transformations soutiennent notre ambition de devenir une entreprise à zéro émission de carbone, à l’avant-garde de la mobilité, en offrant une mobilité sûre, propre et abordable, pour tous, et dans le monde entier”.
Si les véhicules hybrides et électriques sont construits dans un futur proche dans des usines à zéro émission de carbone, on pourra dire qu’il s’agit réellement d’une vraie transition écologique. Reste maintenant à savoir comment fabriquer des batteries sans piller la planète et, surtout, comment nous allons recycler tout cela. Mais c’est une autre histoire…
* Appelé cataphorèse en Europe, ce traitement consiste à plonger la pièce métallique dans un bain de peinture hydrosoluble où elle y est polarisée (en cathode) via un courant électrique permettant de faire migrer et déposer les particules de peinture en suspension dans le bain vers elle. Ce procédé, permet de garantir un dépôt uniforme de la peinture cataphorèse sur la quasi-totalité de la pièce immergée pour la protéger intégralement contre la corrosion.